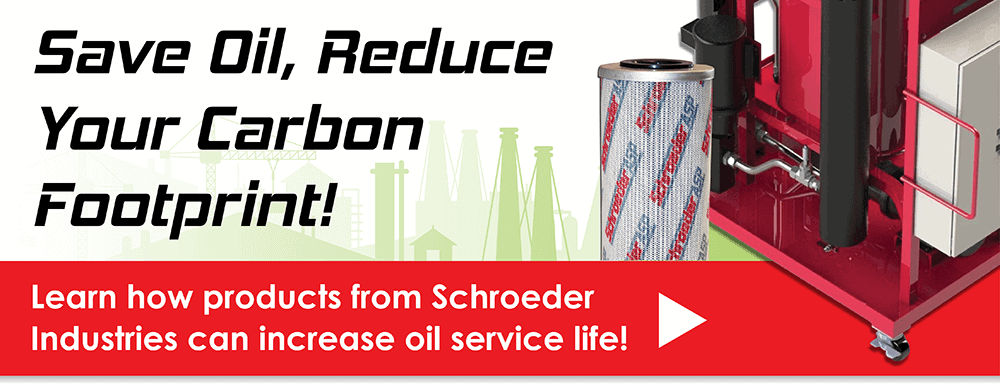
An operation’s carbon footprint is influenced by many factors, and making a business more sustainable requires a combination of solutions. One often overlooked way to increase sustainability is through optimal oil filtration.
All hydraulic oil, turbine oil, and other lubricants have a lifespan, as contamination and the breakdown of chemical compounds degrade oil over time. If contamination is left unchecked, oil reaches the end of its usability much faster.
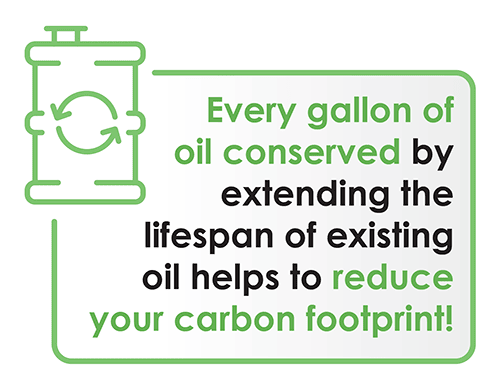
Waste oil is challenging to dispose of properly, and high oil turnover increases demand for the very energy-intensive production of new oil. Much of the hydraulic oil and engine oil in use today is disposed of before its usable life is up.
Every gallon of oil that is conserved by extending the lifespan of existing oil directly contributes to a reduced carbon footprint. So, how do you get the most out of your oil?
Utilizing offline filter systems and high-quality filter elements is proven to extend the lifespan of oil significantly by removing contaminants and slowing the degradation of the oil.
Check out the following case studies where Schroeder Industries products saved a significant amount of oil or extended its service life:
Offline Filter System Saves Manufacturer 2,600+ Gallons of Oil Per Year
A plastic parts manufacturer in the automotive industry experienced frequent failures and downtime in their 16 injection molding machines. Like the majority of hydraulic system failures, high contamination load was identified as the cause. Without a quality control program for the machine oil, the customer changed oil frequently before its usable life was up.
Schroeder Industries stepped in, providing the customer a customized offline filtration system designed to tackle the high contamination:
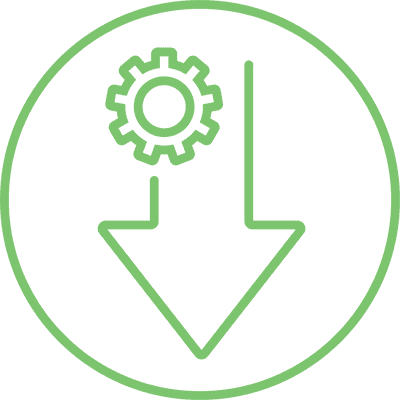
Contamination-Related Downtime Reduced 54%
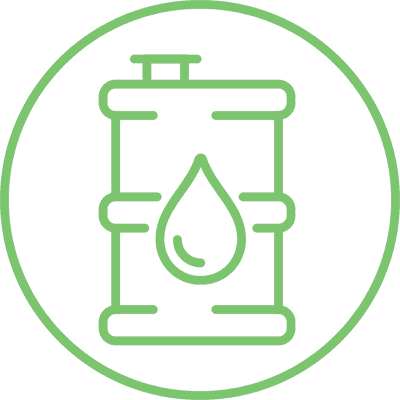
2,600+ Gallons of Oil Saved Per Year
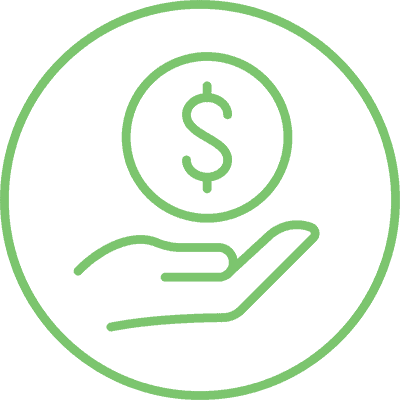
$616,916 Cost Savings Per Year
Specialized Anti-Static Filter Elements Increase Oil Life by 3 Years at Paper Mill
When a paper mill was experiencing a shortened filter element life of just 30 days, Schroeder Industries stepped in to extend the filter life, reduce oil waste, and reduce unscheduled downtime.
An expert investigation revealed the culprit affecting the filter elements: static discharge. Static charges can build up in a hydraulic system due to friction between the fluid and system components. In this case, the static was burning and damaging the elements, causing them to prematurely fail.
By switching to Schroeder’s ASP® Anti-Stat Pleat Media, the electrostatic discharge no longer caused significant problems for the customer. Here are just some of the benefits from this filter element switch:
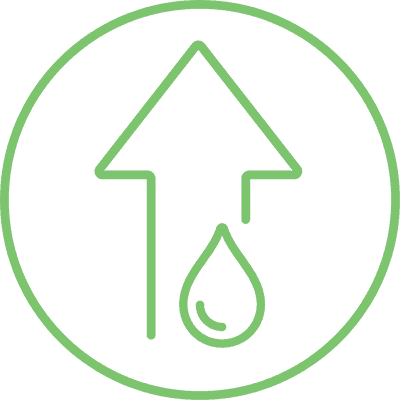
Filter Life Increased +5 Months
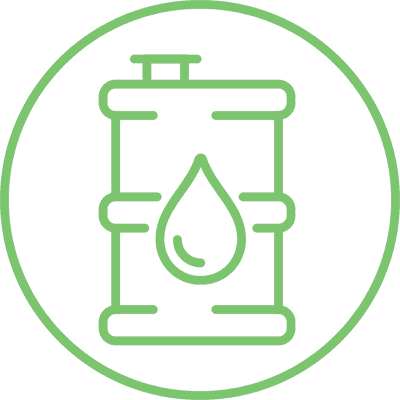
Oil Service Life Increased +3 Years
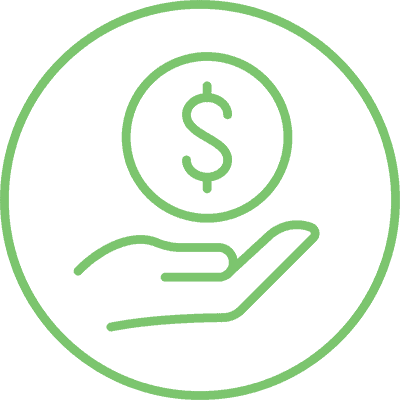
$12.2K Oil Cost Savings Per Year
Varnish Mitigation Unit (VMU) Increases Oil Life by 3.5 Years, Saves Nearly 1,000 Gallons Per Year at Waste Incineration Facility
Operations at a waste incineration plant were constantly disrupted by constant turbine problems on startup.
A survey of 22 machines revealed the issues were the result of varnish buildup in the control block, caused by usage of incorrect oil in certain machines and an inexpensive, ineffective return line filter element. Varnish is a byproduct of aging oil, and is accelerated by contamination, temperature extremes, and other factors.
Schroeder Industries implemented a VMU to continually filter the turbine oil and tackle harmful varnish buildup. This not only reduced downtime and increased productivity, it also helped the customer in the following ways:
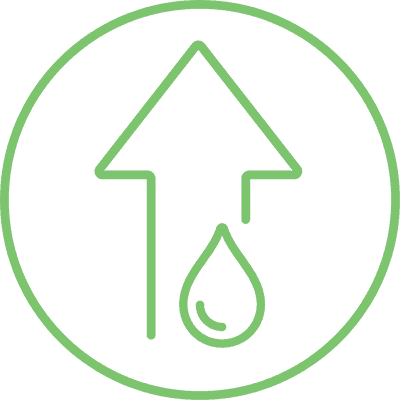
Oil Service Life Increased +3.5 Years
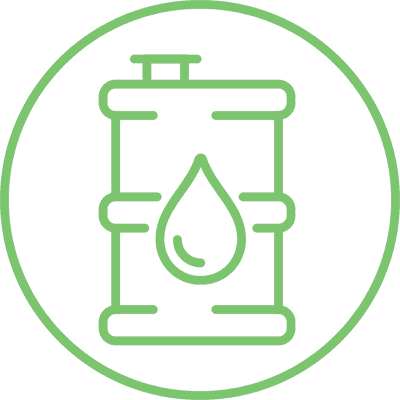
986 Gallons of Oil Saved Per Year
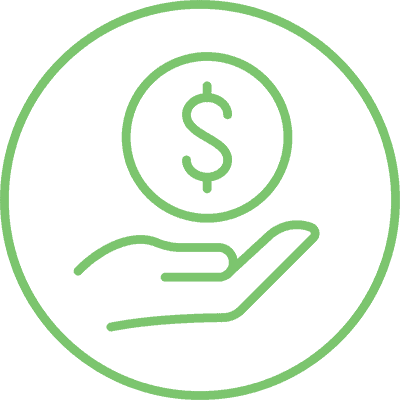
$12.1K Oil Cost Savings Per Year
Schroeder Industries’ Energy Sustainability Initiative
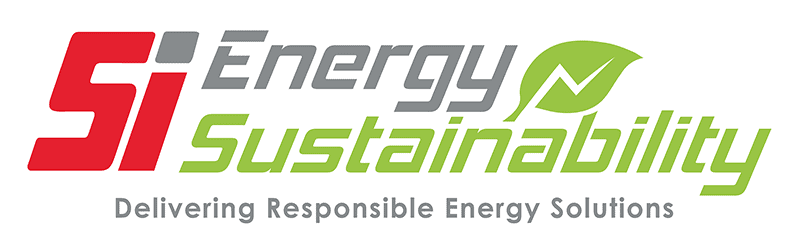
The Energy Sustainability Initiative is Schroeder Industries’ mission to provide fluid power filtration solutions that contribute to a cleaner world and help organizations reach their sustainability goals.
Conserving oil is just one of the ways the products from Schroeder Industries are helping move the world forward towards a more sustainable future. Learn more!
Contact the Experts at Schroeder Industries
If you are experiencing issues such as increased machine downtime, frequent repairs, shortened filter life, and more, the experts at Schroeder Industries can help solve them! Our customers have seen proven increases in oil life and oil-related savings.