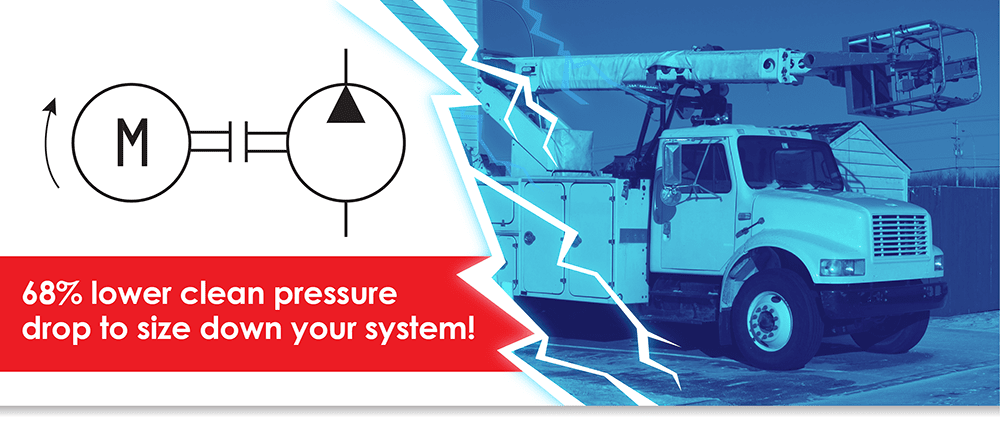
The Future of Hydraulics is Electrifying
In recent years, the mobile hydraulics industry has been revolutionized by the development and proliferation of electric hydraulic systems. Among other inherent benefits, electric hydraulic systems could also be dramatically more energy efficient compared to traditional hydraulic systems.
How is this possible? Unlike traditional hydraulic systems, electric hydraulic motor-pump units only operate when flow and pressure are required to perform the working task at hand.
When there is no flow or pressure required, the electric hydraulic motor-pump unit switches to zero energy-mode, saving the consumption of energy and increasing the system’s efficiency. This is what we call energy efficiency.
Energy Efficiency through Electric Hydraulics
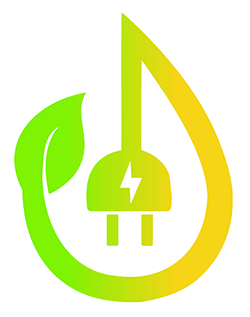
Energy efficiency, put simply, is when less energy is needed for a system to get the job done. This can be achieved by lowering the amount of energy consumed to accomplish an equivalent output (e.g. halt of use when not in operation).
Think about some of the newer car models in the market today.
Some higher-end models shut down every time the car stops at a stop light. Since the car is in idle at that stop light, why would the car continue to place tension and wear the performing components when they’re not performing their sole duty: driving?
This way of thinking is slowly creeping into hydraulics too. Experts are now looking at ways to incorporate these (and other) types of electric energy to power hydraulic machines. This is called electric hydraulics.
Electric Hydraulic Advantages
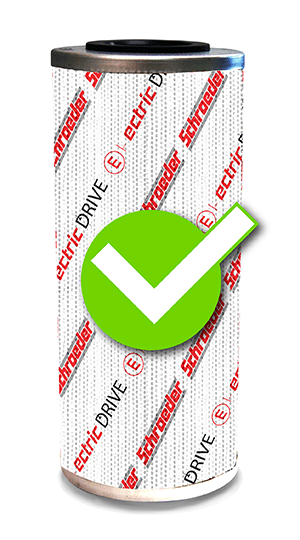
Electric hydraulic systems have some major advantages over their traditional hydraulic counterparts. The key advantages of electro-hydraulic motor pump units are:
- Up to 70% more efficient than standard hydraulic counterparts
- CO2 reduction = less fluid being used in the system
- Component lifespan increased, especially with bearings and seals
- Ability to control direction & amount of hydraulic flow by controlling direction/speed of the electric motor.
- Injection molding machine systems eliminate the need for directional and proportional valves in the motion axis.
- Fewer, less complicated components also simplifies troubleshooting.
- Quieter run times, reducing noise decibel readings
- Save space and reduce weight with lighter, more compact electric systems
- Integrated electrohydraulic packages are now available. These packages include an electric motor, controller, and hydraulic pump combined into one compact unit to lower total cost of ownership.
With the rising trend of electric drive vehicles and utilizing efficient energy throughputs, there is now a need to reduce power consumption and extend the battery life through increased hydraulic efficiency. How do we capitalize on saving energy and becoming more efficient in electric hydraulic systems?
The answer: minimize the pressure drop
Electric Drive Savings Through Pressure Drop Reduction
All energy has a price, and wasting it means wasting meaningful dollars. It is desirable to have as much energy that is inputted into a system available to do useful work. In hydraulic systems, we tend to look at differential pressure across the entire system. Differential Pressure describes the loss of energy available in a hydraulic system—however, the energy is not lost, but converted into thermal energy, which is unavailable to perform useful work.
For example, a small pressure drop effects high horsepower systems, as the pump/motor group must make up for that loss of energy and operate much harder, costing more money and shortening component life. Take a look at the figure below to see an example of how much money can be saved by lowering the pressure drop by a few psi:
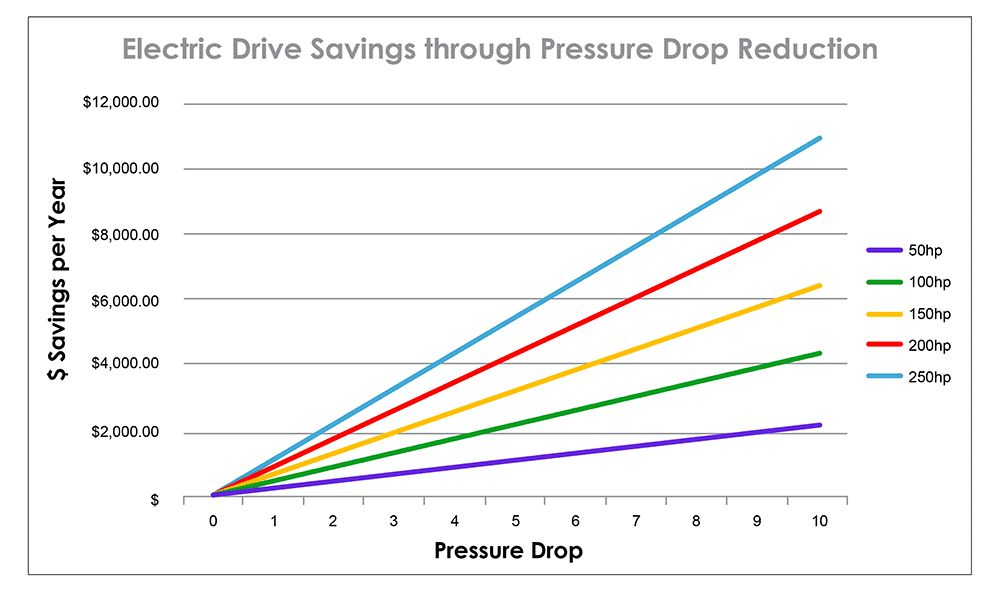
So how do we lower the overall pressure drop in an electric hydraulic system? That is where Schroeder’s Electric Drive media can help.
Schroeder’s Electric Drive Media
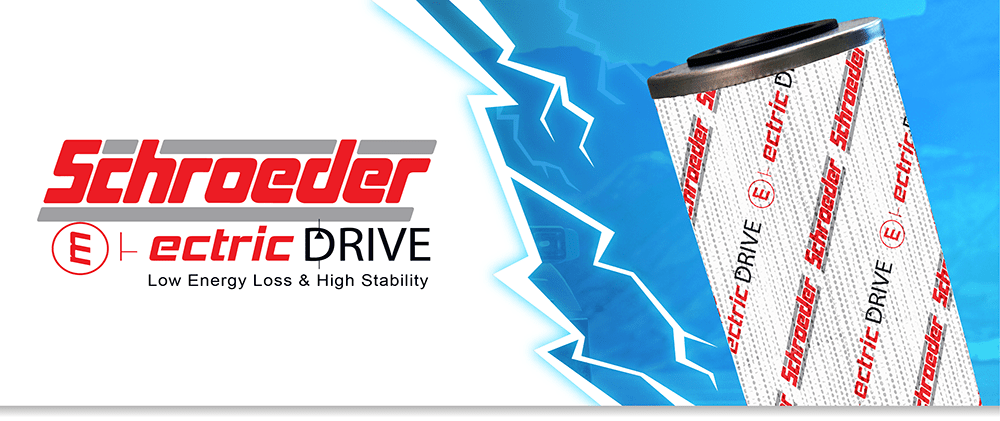
The use of Schroeder’s GREEN, Electric Drive (E-Drive) Media filtration technology guarantees safe and reliable equipment operation, all-while conserving the use of energy.
Part of Schroeder’s Energy Saver initiative, filter elements made using the all-new E-Drive Media are characterized by a low pressure drop, making them suitable for low energy requirements compared to conventional hydraulic elements under the same ambient conditions.
In certain applications, the E-Drive Media can lower the pressure drop to a point where consumers may be able to size down their horsepower requirements on their current motor and save even more overall!
E-Drive filter elements are made using an all-new specialty formulated, high efficiency, low differential pressure media and are the perfect choice for use in electric hydraulic drive motor-pump units. Use them for conserving energy bills and wherever high viscosity fluids are employed – especially at low temperatures that produce a cold start behavior.
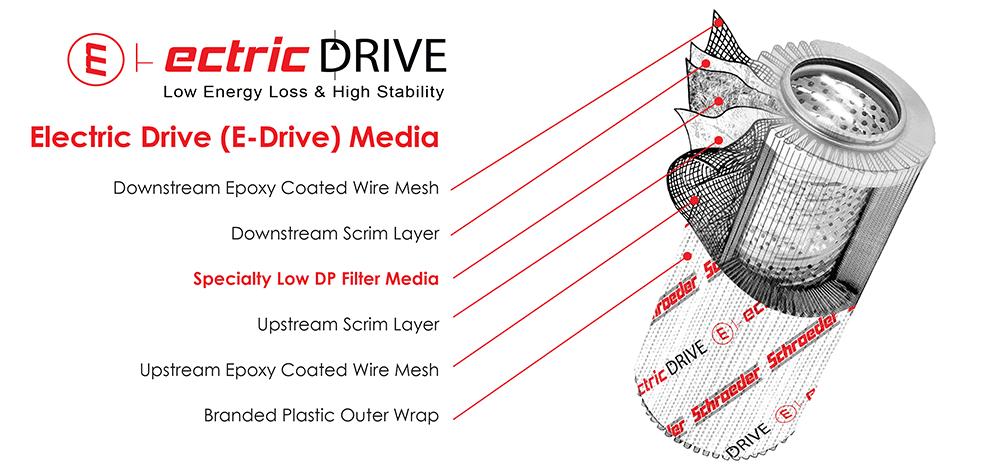
Let’s see how our 10-micron Electric Drive media element compares to the typical synthetic microglass media available on the market today.
Technical Specs (evaluated in K-sized element):
Media Type | β200 [µm(c)] | Pressure Drop Factor [psid/gpm] |
E-Drive Media (10 µ) | 10.2 | 0.050 |
Typical Synthetic Media (10 µ) | 10.6 | 0.156 |
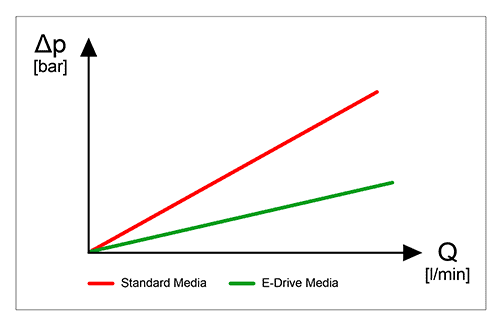
- Element Collapse Rating: 145 psid (10 bar)
- Temperature Range: -22°F to 212°F (-30°C to 100°C)
- Flow Direction: Outside to Inside
E-Drive Media is currently rated for 10-micron filtration, with other micron options available in the near future.
What Can E-Drive Media Do For You?
To see if Schroeder’s Energy Saving Initiative E-Drive Media can be the right solution for your electric hydraulic systems, email us at sisales@schroederindustries.com or leave a comment in the blog post below.
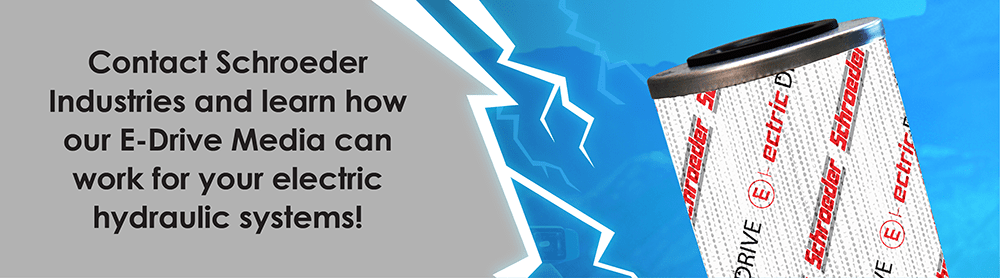
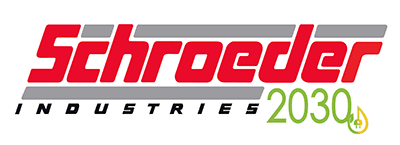
E-Drive Media is part of Schroeder Industries’ 2030 Initiative, a suite of filtration solutions and technology proven to support carbon neutrality goals. Learn more about how Schroeder Industries and sustainability go hand in hand!