Eliminate Hidden Contaminants with Ultimate Roll-Off Cleanliness
Leave a Comment
Equipment failures within warranty and product recalls are a major headache for both end users and manufacturers, ranging from costly and inconvenient to downright dangerous. One common cause of issues and even catastrophic failures is contamination present in the equipment the moment it exits the assembly line.
Just last month, Toyota recalled tens of thousands of trucks and SUVs due to possible machining debris in the engines, which could result in anything from knocking and rough performance to total loss of engine power.
A similar machining debris issue caused an even bigger recall of over 1 million Hyundai and Kia vehicles in 2017, as well as triggering a costly class action lawsuit brought by end users.
The risks of contamination-related, premature equipment failures to both end users and original equipment manufacturers are clear. So, how can these issues be prevented?
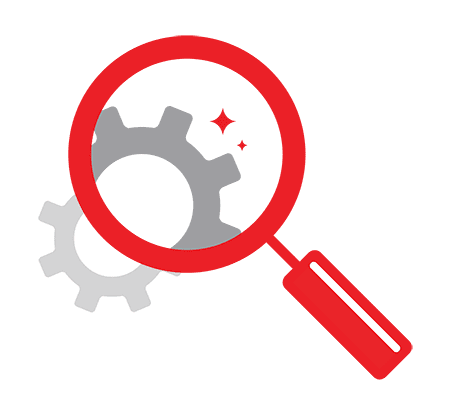
What is Roll Off Cleanliness?
Roll off cleanliness is commonly referred to as the overall contamination level of the fuel system, hydraulic system, and hydraulic fluid in the equipment at the time of release from an assembly line or re-build line, after testing and before shipping to customers and/or end users.
Built-in contamination, or contamination that enters a vehicle or piece of equipment during assembly, is a common cause of premature failure. A high standard of roll-off cleanliness ensures that new equipment is free of contamination which can cause failures within warranty, triggering returns, recalls, and other negative outcomes that inconvenience consumers and impact a brand’s reputation.
Where Does Built-In Contamination Come From?
For hydraulic, lubrication, and fuel systems with sensitive components, even contaminants measured in microns can cause damage. For optimal roll-off cleanliness, there are several avenues of contamination that must be monitored and addressed, depending on the application:

Machining Debris
As the automotive manufacturers mentioned above are all too aware, machining debris, or particulates left over from the process of manufacturing and assembling components, can be catastrophic.
Tiny fragments of metal and other particulates produced in the manufacturing process can cause both localized damage to engines or critical system components and spread downstream of the original contamination source, causing wear and tear throughout the system.
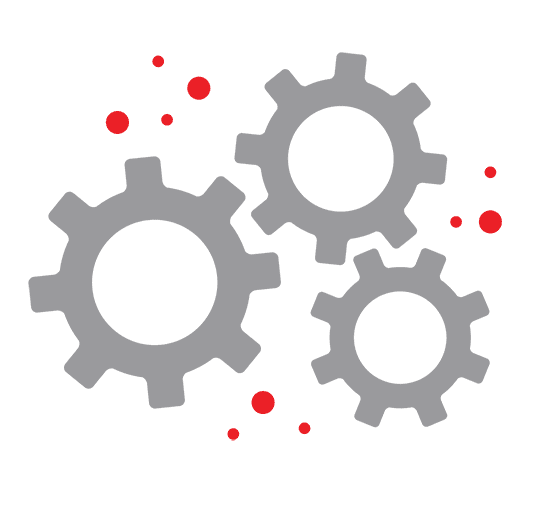
Environmental Component Contamination
The overall cleanliness of the manufacturing setting at every stage of production is also vital for ensuring overall roll-off cleanliness. Dust, debris, and moisture present in the environment can settle into components as they are being manufactured, packaged, transferred, or assembled.
Most manufacturers source at least some components from third party vendors, so the condition of other facilities should also be examined, and incoming components should be tested to ensure they comply with a manufacturer’s standard of cleanliness.
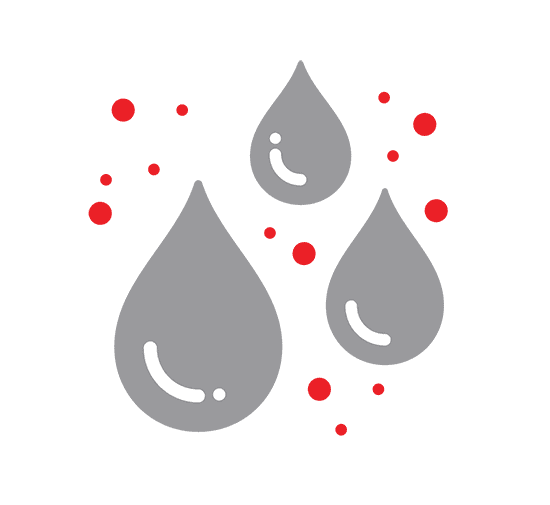
Contaminated Hydraulic and Lubricating Fluid
Contamination from newly added hydraulic or lubricating fluids is another common source of contamination at the start of a machine’s life. Oil producers generally adhere to strict ISO standards, but throughout the process of production, transfer, and filling, contaminants may ingress into the hydraulic fluid.
New oil should be tested before being added to any system. It is also recommended to utilize an offline filtration system or kidney loop filter to cycle the oil through the system and ensure its cleanliness.
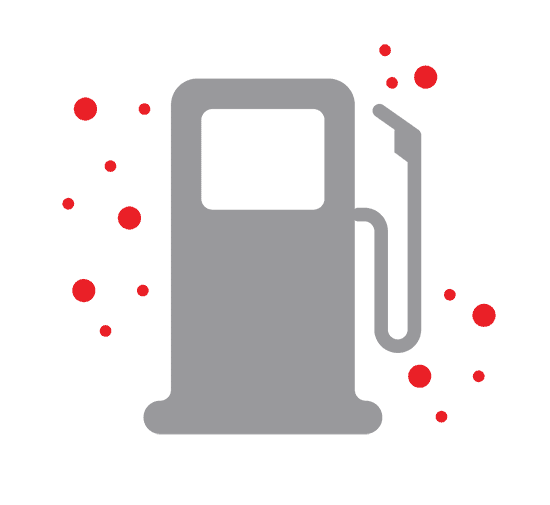
Contaminated Fuel
For plants which produce diesel-powered mobile equipment, fuel management for on-site testing and end-of-line filling equipment is a critical part of their operations. Fuel is a common vector for water, bacteria, and particulate contamination to enter a fuel system, as there are many potential points of exposure throughout the fuel production and transfer processes.
Inbound fuel, on-site storage tanks, and distribution systems should be carefully monitored and filtered. Filtration units specialized for maintaining diesel quality are a must to ensure clean fuel, protecting new equipment from an influx of contamination into the fuel system.
Schroeder Industries’ Roll Off Cleanliness Arsenal
Schroeder Industries understands the importance of setting end users up for success through roll-off cleanliness. We offer a variety of filtration solutions and diagnostic tools that ensure your equipment is putting its best foot forward from a cleanliness standpoint when it leaves the assembly line.

Component Cleanliness Testing Cabinets
Testing cabinets like Schroeder’s CTU 1000, CTU-SC, and CTU-EB are used to analyze individual machine components and provide detailed analysis of the type, size, and quantity of contaminants. Analyzing components throughout the production, storage, and system assembly process ensures that individual contaminants are clean when entering the equipment.
If a testing cabinet is outside your budget, Schroeder Industries offers turnkey testing services and expert analysis!

Filter Cart Systems
Contaminated hydraulic fluid or oil is a common cause of premature machine failure. Offline filtrations systems such as Schroeder’s array of filter carts (including the MFS, FS, and AMFS) allow for flexibility and mobility when testing the hydraulic fluid and lubricating oil across a variety of machines.
Ranging from streamlined-but-reliable basic cart systems to advanced systems with onboard particle counting and recording capabilities, these filter carts ensure the cleanliness of fluid within the equipment and can be customized for your specific needs.

Hand Held Hydraulic Filter Units
For an ultra-portable alternative to a filter cart system, Schroeder Industries offers hand-held filtration units like the HFS-15.
These lightweight, hand-held units provide the same powerful filtration as a filter cart system with unprecedented mobility.

Portable Fluid Sampling Systems
Diagnostic tools like the TFC are used for establishing ISO counts for fluids in real-time. Due to the technology included in the TFC, it is able to distinguish air bubbles from particulate contamination, removing the counted air from the particle count, thus providing a more accurate ISO code. With shape and size recognition software, determining the type of the contamination present in the hydraulic fluid is now even easier.
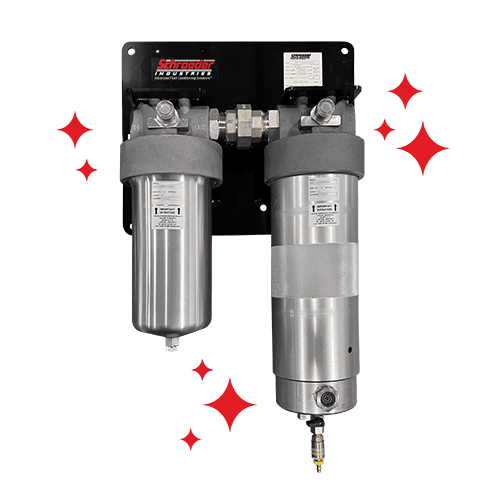
Bulk Diesel Filters
Schroeder’s Fuel Filtration division specializes in coalescing and particulate filtration for diesel fuel.
Products like the BDF, GHCF, and more provide superior filtration at every stage of the fuel supply chain, including during transfer, point of fueling, and kidney loop circulating filtration for bulk storage tanks.
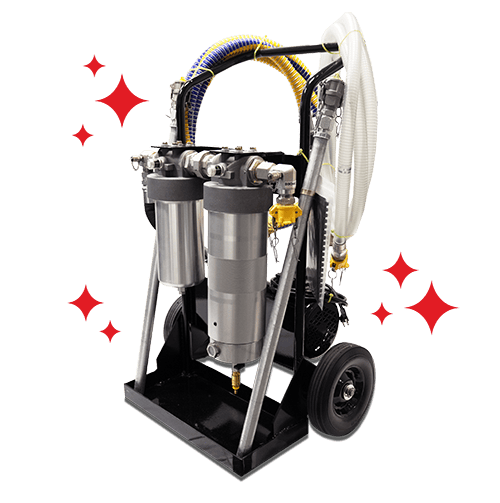
Mobile Diesel Filtration Units
Fuel filtration carts like the BDFC combine our world-class fuel filters with integrated pumps, hoses, and a mobile cart chassis.
These turn-key, complete systems offer increased flexibility and enable easy transitions from application to application around a manufacturing plant or storage facility.
Schroeder Industries’ Commitment to Cleanliness
Your partner for cleaner parts!
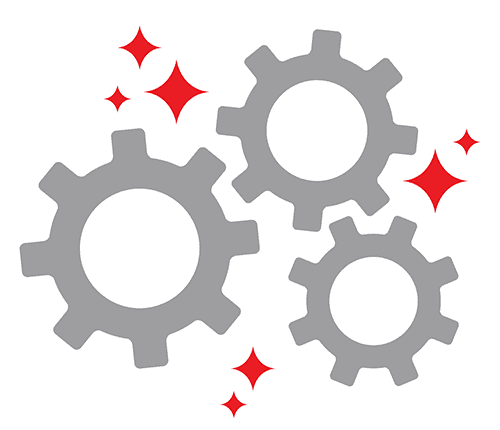
As a provider of critical filtration components and accessories, Schroeder Industries is all-too aware of the importance of providing clean parts to our manufacturing partners.
Our manufacturing facilities in Leetsdale, PA and Cumberland, MD maintain high standards of cleanliness, creating a comfortable working environment and minimizing the risk of particulate contamination.
Our products are subject to stringent standards which include proprietary, rigorous testing and cleaning methods that ensure our filters, rotomolded reservoirs, and other components arrive to our partners in clean condition.