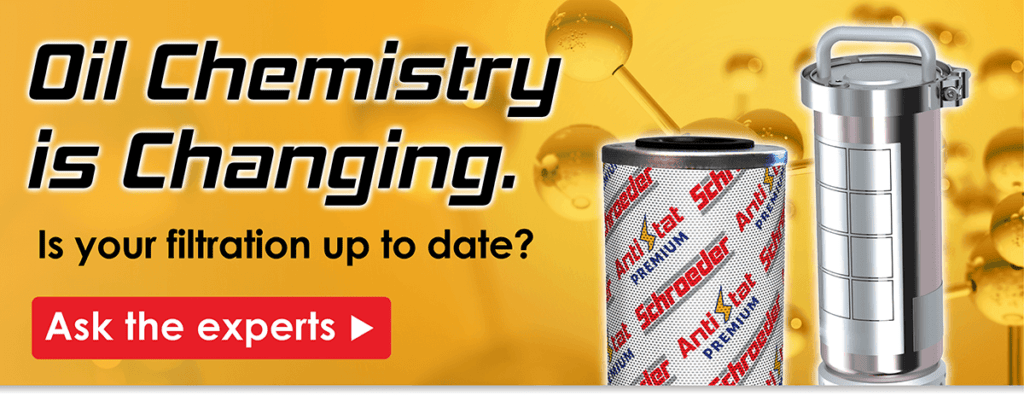
Why is Oil Chemistry Changing?
For decades, Group I oils dominated the market for hydraulic and lubricating fluid, particularly for industrial applications. Because they are created through a simpler refining process, they are the least costly hydraulic base oils available. However, the chemical composition of these less refined oils can have consequences for the environment and even potentially for the workers exposed to them.
Group I ‘Lightly Refined’ Oils have been deemed an environmental hazard.
Group II & III ‘Hydrocracked’ or ‘Synthetic’ oils are replacing Group I oils as a more eco-friendly alternative.

Between 2012 and 2020, the market share of Group I oils halved. As environmental concerns drive industry standards towards more eco-friendly ends, this trend is expected to continue. But while this transition towards Group II and Group III oils benefits environmental and worker safety, there are some impacts on hydraulic equipment that operators must account for.
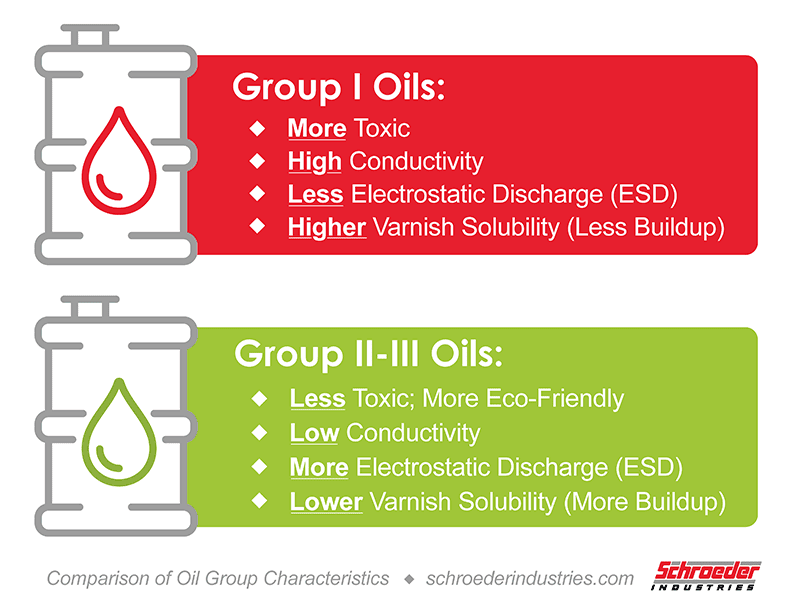
Increased Electrostatic Discharge (ESD)
Traditional Group I oils, with their higher concentration of heavy metals, have relatively high conductivity. Due to the higher conductivity, static charges generated by friction between the oil and filter element are more easily dispersed.
In Group II and Group III oils, these heavy metals have been removed, which lowers their conductivity. As a result, electrostatic discharge (ESD) can build up to potentially damaging levels. This can have serious impacts on the condition of the hydraulic system, and even pose a hazard to other electrical systems or even personnel in close vicinity to the affected equipment.
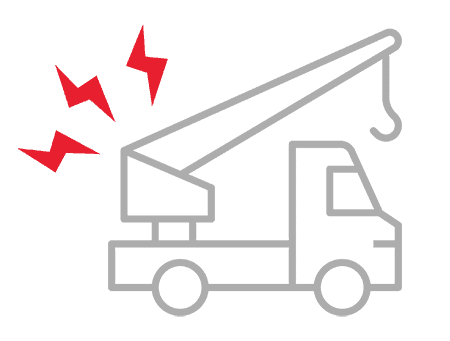
Schroeder Industries Solutions for Static:
To combat the increasing presence of ESD in hydraulic equipment, Schroeder Industries developed cost-effective solutions for moderate and major cases of static buildup.
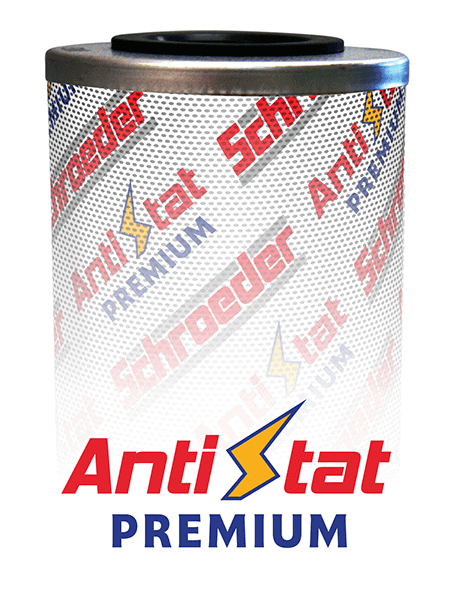
Anti-Stat Premium: Supercharged Static-Busting Capabilities For Extreme ESD
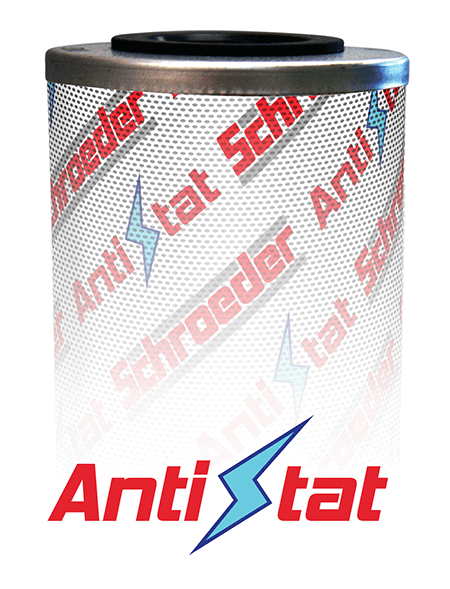
Anti-Stat Media: Reliable, High-Performance Solution For Low to Moderate ESD
Increased Varnish Buildup
Another side-effect of the reduced conductivity in Group II and Group III oils is the increase of varnish formation. Due to the lower conductivity, oxidation is more likely to occur, causing the oil to deteriorate into sticky compounds that settle throughout the hydraulic system—not unlike plaque in human arteries. This has a variety of impacts on the functionality and condition of the hydraulic system including:
Schroeder Industries Solutions for Varnish:
Bust varnish before it can tarnish your equipment! Schroeder Industries offers a series of filtration solutions specifically targeting varnish and varnish precursors, including:
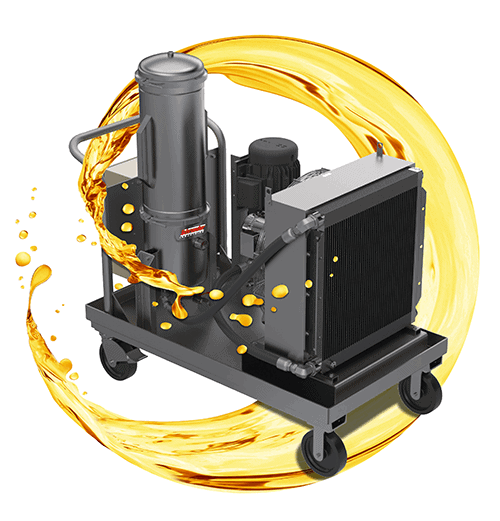
VEU – Varnish Elimination Unit
The service-friendly Varnish Elimination Unit (VEU) is used to prepare mineral oils and is particularly effective at removing varnish.
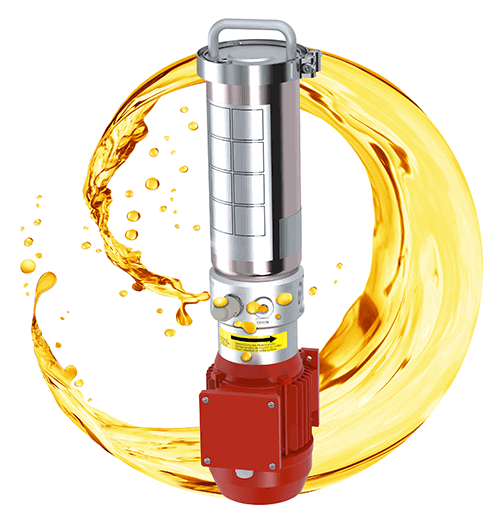
New in 2024: The VEU Compact
A highly efficient, cost-effective, compact unit with world-class varnish elimination capabilities.