Boost Your Equipment Hardiness Through Cutting-Edge Fluid Testing
Leave a Comment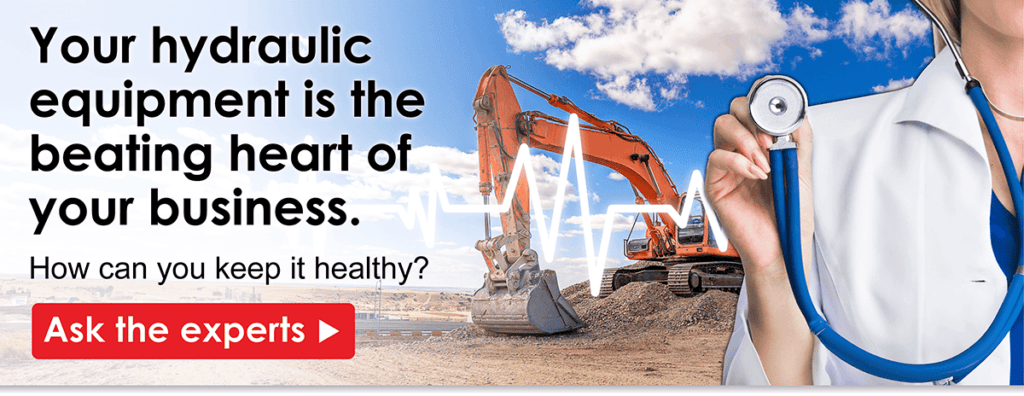
When you think about it, a hydraulic machine is a bit like a human body.
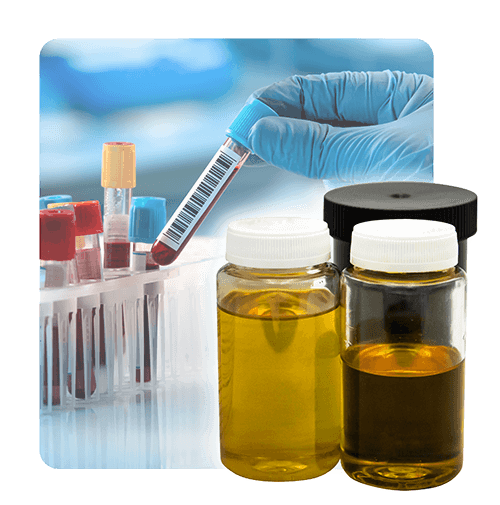
The motor and pump act as the equipment’s heart, driving the oil throughout the hydraulic system like blood in a person’s veins. When a person is feeling unwell, or are monitoring an ongoing medical condition, blood testing gives critical insights into what is happening inside their body and helps chart a path forward for their care.
Just like a blood test does for a human being, a fluid sample is the best way to begin assessing the health of your equipment and diagnosing any underlying issues related to contamination.
Some of the most common causes of equipment inefficiency, failure, and reduced lifespan of components come down to contaminants and varnish that build up in the oil and travel throughout the machine’s ‘body’. In fact, it’s estimated that over 70% of hydraulic system failures are related to fluid contamination. Fuel sources and process fluid are also susceptible to damaging contamination.
Schroeder’s Oil Analysis Program offers a simple way to stay on top of the health of your equipment!
Whether your operation has only a handful of machines, or you manage a massive fleet, Schroeder Industries offers an array of accurate lab testing services and easy digital tracking that keep you informed of your machine’s health.
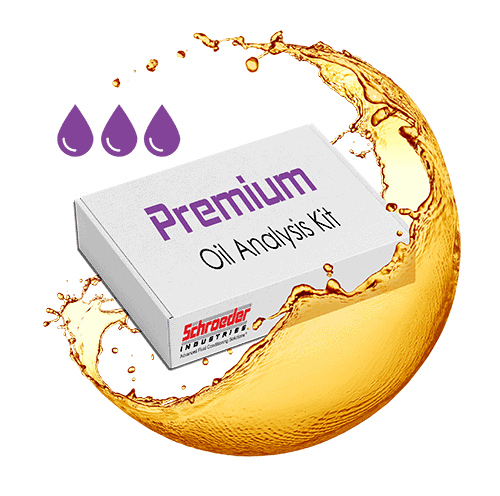
To satisfy virtually every application, Schroeder Industries offers several different test kit options, all backed by the powerful Fluid Care Portal.
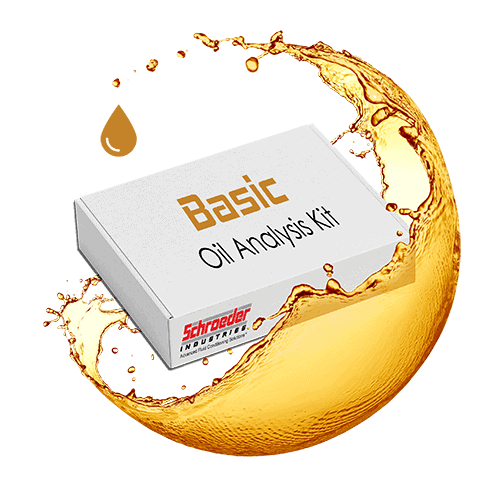
Basic Analysis Kit
Our most cost-effective testing option, focusing on the most essential fluid condition factors.
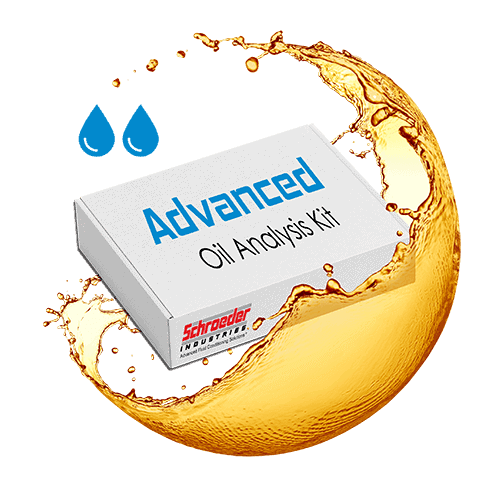
Advanced Analysis Kit
Achieve deeper understanding of your fluid condition with a more expansive testing package.
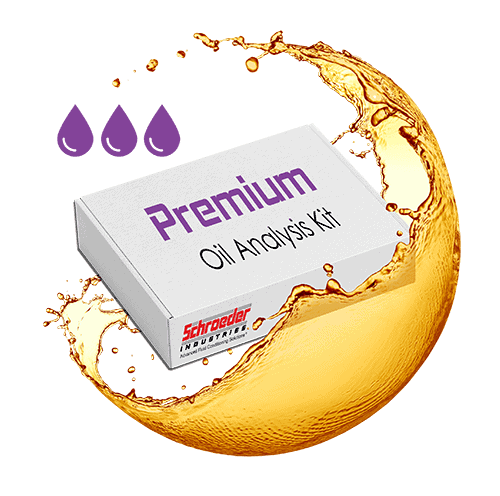
Premium Analysis Kit
Our most comprehensive testing kit, for the most advanced insights into your fluid.
How does the Fluid Care Portal enhance your fluid analysis program?
Regular testing is vital for monitoring trends in your fluid health and preventing problems before they arise. However, tracking results over time for many pieces of equipment takes time and hassle. As part of our testing and fluid analysis services, Schroeder Industries is now offering a smart digital solution for detecting trends in the quality of your hydraulic oil, diesel fuel, process water, and more.
Part of Schroeder Industries’ Oil Analysis Program, the Fluid Care Portal is a new, powerful digital tool for easily tracking the health of your equipment’s fluid as you test over time:
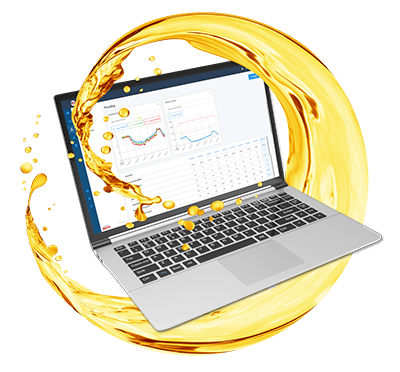
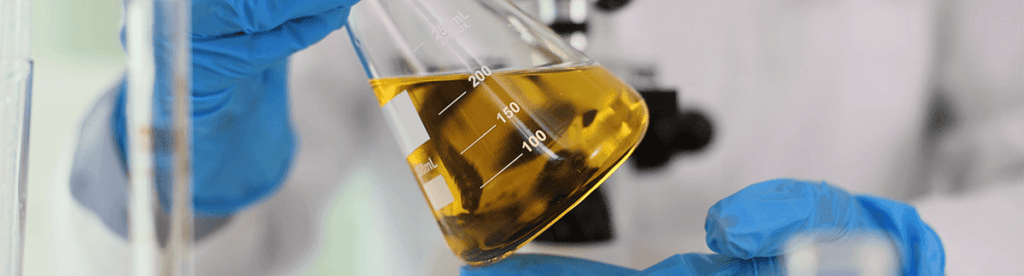
Ask The Experts In Fluid Analysis!
Tell us about your application and fluid cleanliness goals, and find out which kit is right for you: