Quality Protection Filter Elements Offer Superior Defense from Contamination
Leave a Comment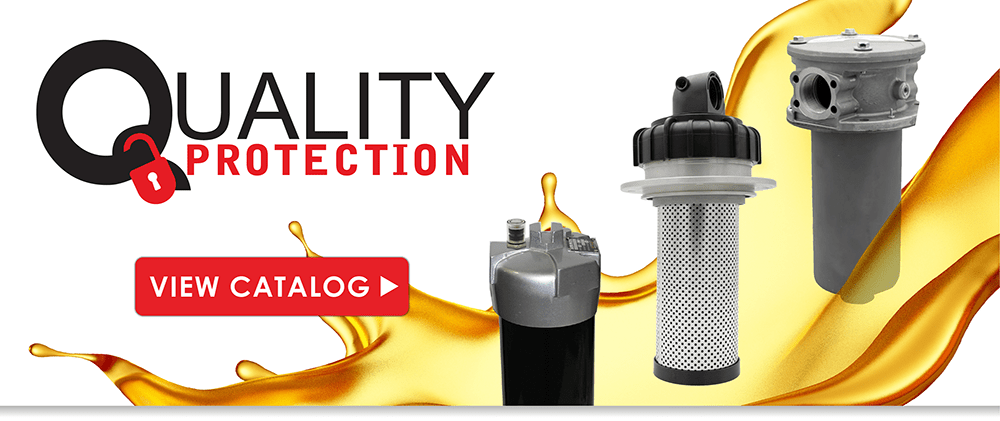
‘Will-Fit’ Doesn’t Cut It
Keeping a hydraulic system free of contamination is critical for system efficiency and longevity, and high quality filtration elements are the key to contamination control. Unfortunately, it’s not uncommon for customers to seek out low-cost, off-brand imitations of Schroeder Industries filter elements in order to cut down on expense.
Not all filter elements are created equally, and just because a given element fits in a Schroeder filter housing, it doesn’t necessarily provide adequate filtration. Cut-rate imitations may claim that “All filtration elements are guaranteed to meet or surpass all specifications of the original equipment manufacturer” but that’s not always the case. Take a look at the numbers below and see for yourself:
Elements | Schroeder KZ5 | “Will-Fit” replacement |
# of pleats | 80 | 71 |
Pleat Height (in) | 0.63 | 0.61 |
Media Layers | 6 | 5 |
DHC (g) | 119 | 84.3 |
Beta 200 | 4.8 | 12.2 |
Beta 1000 | 6.3 | 18.1 |
Elements | Schroeder 27KZ1 | “Will-Fit” replacement |
# of pleats | 80 | 71 |
Pleat Height (in) | 0.63 | 0.61 |
Media Layers | 6 | 5 |
DHC (g) | 378.1 | 233.1 |
Beta 200 | <4 | 12.4 |
Beta 1000 | <4 | 18.3 |
Cheaper knockoff filter elements trade functionality for lower cost, exposing the hydraulic system to increased risk of contamination, machine downtime, and system failure. Furthermore, the blame for these failures may be wrongly placed on the housing manufacturer, not the cut-rate filter element.
How can we ensure that proper, high-quality filtration elements are being used?
Quality Protection: Guaranteeing High Quality Filter Elements, Every Time
Quality Protection is Schroeder’s answer to the problem of mismatched, inadequate elements. The patented, premium Quality Protection elements are engineered specifically for superior performance when paired with Schroeder filter housings.
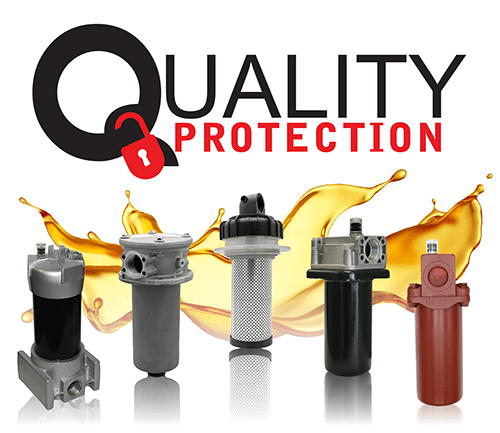
What does Quality Protection mean?
- End users cannot substitute “will-fit”, low quality elements for a Quality Protection element
- OEM’s will capture aftermarket revenue from Quality Protection elements; exponential growth year after year
- Increase in machine productivity and reliability when Quality Protection filtration elements are deployed
- Overall reduction in warranty claims when hydraulic equipment is protected by superior filtration
Why Do My End Users Need Quality Protection?
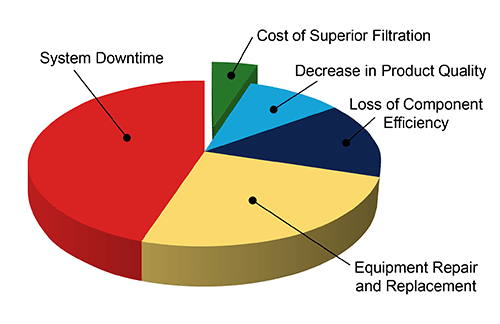
Hydraulic system downtime and repairs represent a significant portion of overall costs to equipment end users. Contamination is the leading cause of hydraulic machine downtime, accounting for as much as 70% of premature machine failures. Ensuring the highest quality filtration protects your end users’ equipment from contamination-related failures and associated costs.
How Does Quality Protection Benefit My Business?
Quality Protection is the clear choice for protecting your end user’s hydraulic equipment from contamination-related damage, but how does it benefit your business directly?
Not only will your equipment perform at like-new levels, but Quality Protection can also provide an increase in aftermarket retention year over year. By taking advantage of our Quality Protection filter elements with the private labeling option, you may see up to 90-100% aftermarket retention. Compare this to the expected retention when using standard Schroeder elements with or without private labeling.
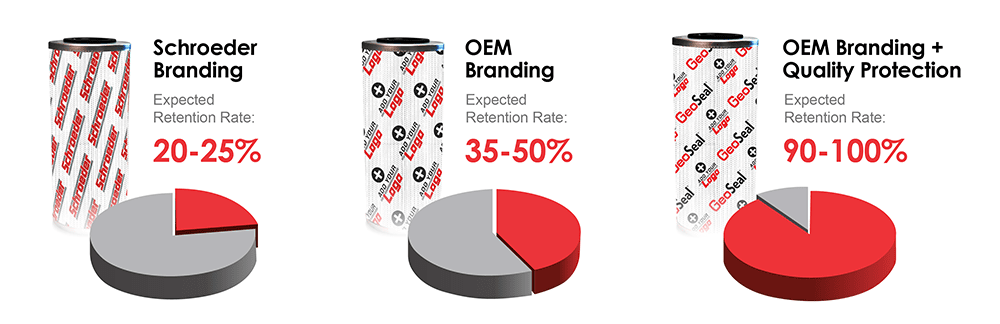
Over a 10 year period, one may sell an estimated triple the quantity of filter elements when implementing a Quality Protection strategy than without. The associated boost to sales margins makes this a highly profitable, winning strategy.
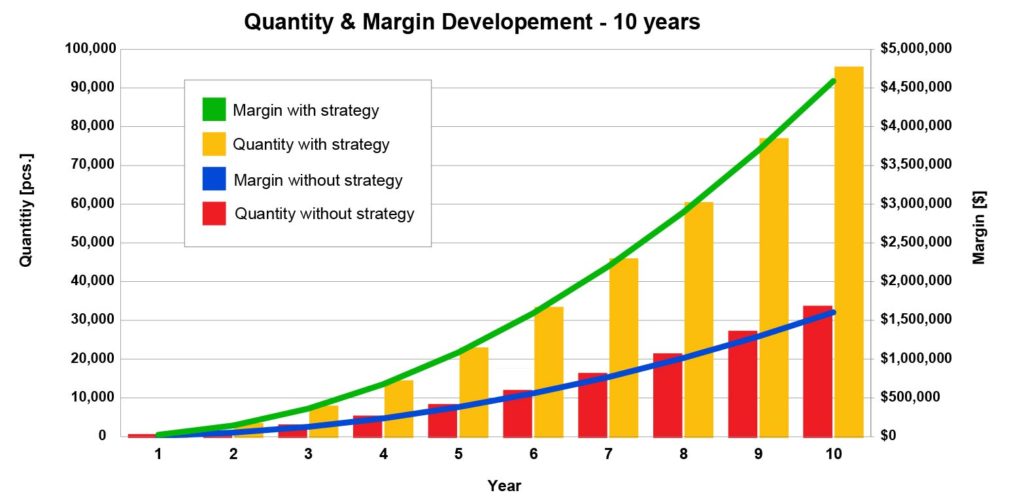
Quality Protection Solutions
Private Labeling Solutions
Incorporating a private labeling program has proven benefits for aftermarket element business retention, and offers additional protection against inferior, cut-rate filter element substitutions. Schroeder offers a full line of branding solutions for filter elements, including our Quality Protection items. Review our Private Labeling Capabilities Form and email sisales@schroederindustries.com to plan your private labeling program!
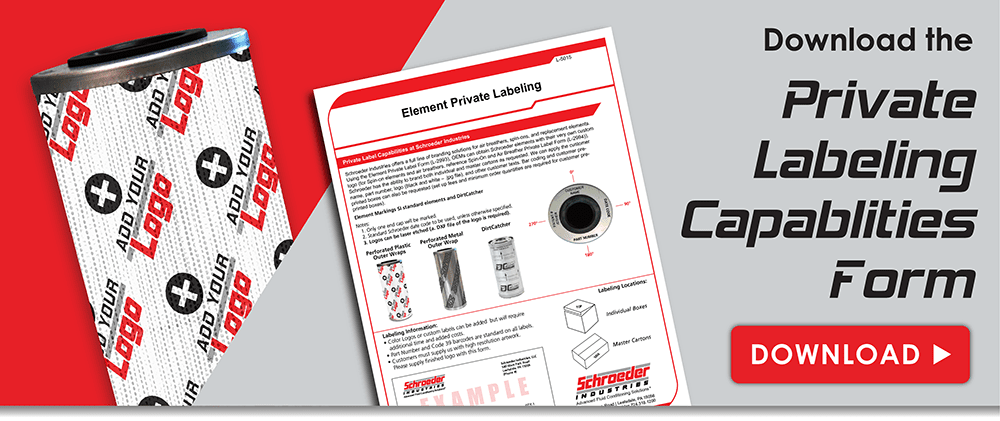
Protect Your Equipment with Outstanding Fluid Contamination Analysis
Leave a Comment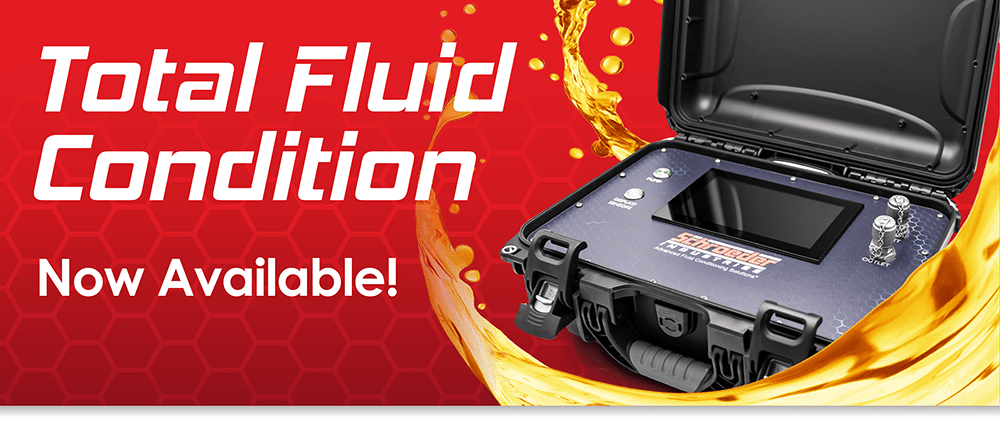
Mitigating fluid contamination is a chief concern for hydraulic systems. Solid, liquid, and other forms of fluid contamination account for up to 90% of all hydraulic system failures. Water, ingested particulate contamination, and metal particles from internal component wear are just a few types of contamination. Contamination is influenced by ambient conditions and other variables, and can have serious impacts on hydraulic equipment performance.
Contamination cannot be completely stopped, but proper fluid filtration can prolong the lifespan of your hydraulic components—and a successful treatment strategy begins with accurate diagnostics.
Portable Fluid Condition Monitoring
To make fluid assessments more convenient, Schroeder Industries developed several portable fluid condition monitoring systems. These compact units are designed to deliver real-time insights into the health of a variety of hydraulic fluid types. On-site analysis with a portable condition monitoring unit saves time and money compared to shipping samples to oil testing labs, or using complicated analysis kits. Their portability makes them usable in the field, in remote locations, along a manufacturing process production line—anywhere a hydraulic system can be found.
Introducing Total Fluid Condition (TFC)
The new TFC unit represents the latest in fluid condition monitoring technology. This revolutionary portable service unit is designed to measure and differentiate particulate contamination, as well as relative water content and temperature.
Improving Contamination Data Accuracy
Correctly identifying the type and source of hydraulic fluid contamination is critical for developing a treatment strategy. The TFC unit improves upon the accuracy of fluid contamination data in synthetic and mineral oil based hydraulic fluids, offering users a more complete analysis of their fluid health than was previously possible. This improved precision stems from the new direct digital imaging sensors incorporated into the TFC units.
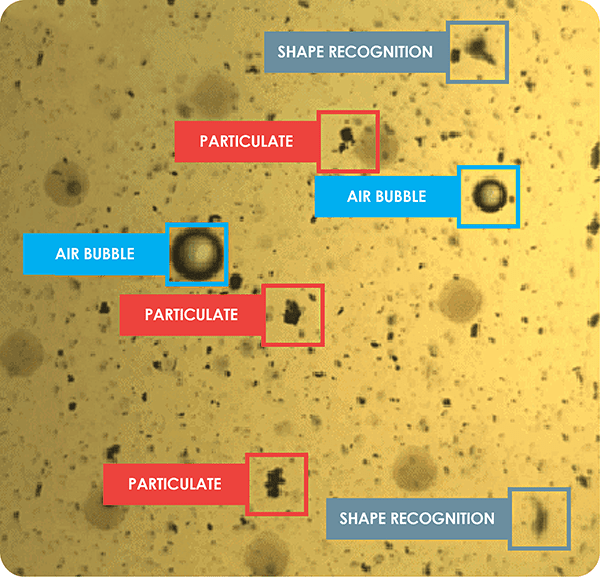
Other portable fluid contamination monitoring units have utilized light-based sensors, which struggle to differentiate between contamination types, but direct digital imaging sensors can distinguish air bubbles and water molecules from solid particles. This results in a more accurate ISO count, and better understanding of the fluid’s health.
The TFC can also sort particles into fatigue, cutting, sliding wear, and fiber categories to estimate cause of contamination. The direct imaging particle counting software coded into the unit uses size and shape-recognition technology, based on advanced algorithms, as a dirt classifier to distinguish contaminates.
TFC Applications
Like Schroeder’s other portable fluid diagnostics systems, TFC is a powerful, versatile tool for any fluid cleanliness testing scenario:
- Perfect for in-plant/industrial applications, during the assembly process or at the end of the production line.
- The compact design and onboard battery also make the TFC ideal for mobile applications, such as testing for service trucks or in remote locations.
Other Benefits of Fluid Condition Monitoring
The oil waste reduction aided by the TFC unit’s fluid diagnostic capabilities doesn’t just help protect your equipment. It also reduces costs and environmental impacts related to oil waste.
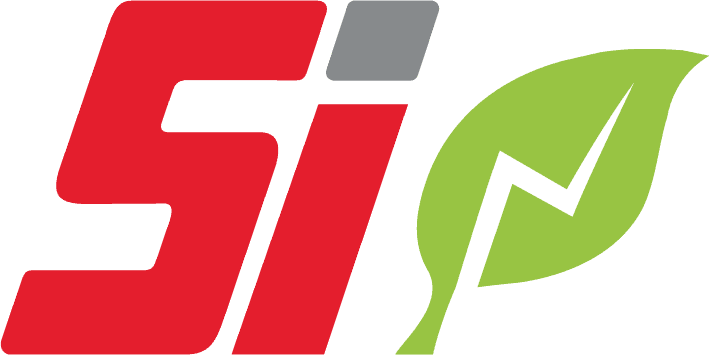
All hydraulic fluid must be changed eventually, but routinely testing fluid cleanliness and addressing contamination prolongs its lifespan. This results in less frequent oil disposal, saving on the expense of new oil.
Additionally, the reduction in hydraulic oil waste and consumption helps lower an operation’s carbon footprint and environmental impact. The TFC unit is part of Schroeder Industries’ Energy Sustainability Initiative supporting carbon reduction goals across various industries, thanks to the benefits it imparts by helping extend the life of oil and reduce waste.
Want to learn more about what Total Fluid Condition can do for your business? Contact us!
sisales@schroederindustries.com
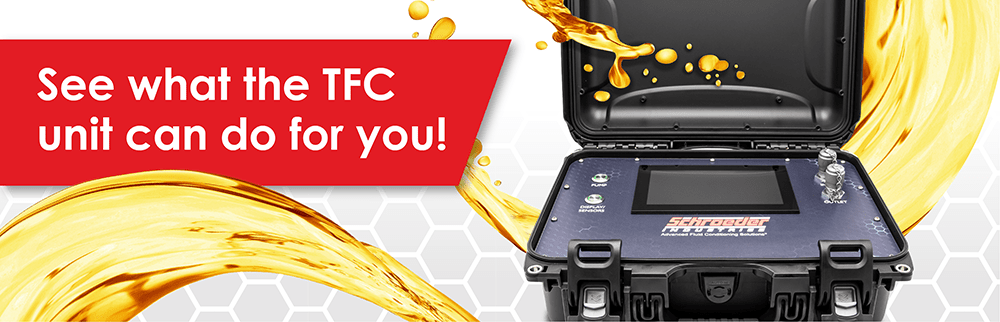
Confused about Hydraulic Filtration? Breakthrough to Premium Hydraulic Know How!
Leave a Comment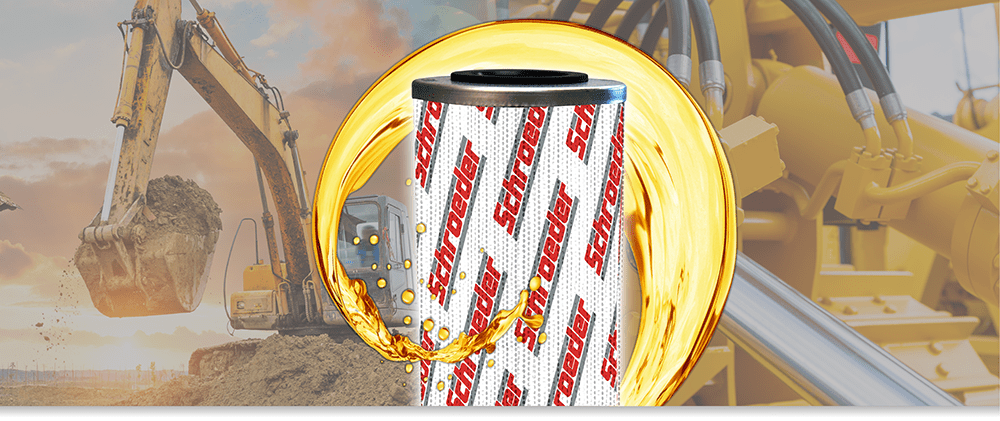
Anyone involved in the industrial field has likely come across the term “hydraulic filtration” before. But, what is it?
Hydraulic systems and machinery operate by applying pressure to dense fluids or oils, called hydraulic fluid, in order to transfer mechanical energy to other components within the system. Some examples of equipment that utilizes hydraulics include heavy machinery like backhoes and cranes, vehicle braking systems, and even theme park rides.
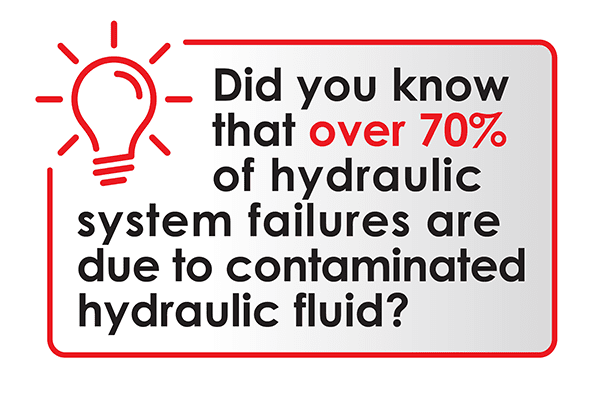
However, hydraulic fluid is at risk of contamination. Particles that are smaller than what is visible to the human eye are able to sneak into a hydraulic system and cause damage to internal components, leading to expensive repairs. Over 70% of all system failures are caused by contaminants in the hydraulic fluid. Even when no immediate failures are apparent, high contamination levels can be present and sharply decrease hydraulic controls in the blink of an eye.
Types of Contamination
Contamination can come from two basic sources. It either enters the system from outside (ingestion) or are generated from within (ingression). Types of contamination include:
- Air
- Water
- Microbial Growth (Yes, microbes can grow in hydraulic fluid!)
- Varnish, which can be caused by degraded oil
- Particulates, including ingested dirt or degraded particles from internal system wear
Contamination Control Through Hydraulic Filtration
Contamination cannot be completely stopped, but it can be managed. Hydraulic filtration is what “cleans” contamination from the operating fluid in equipment. Specially designed hydraulic filters are used for removing contaminants from fluids and safely disposing of them without causing harm to the equipment.
Contamination control through filtration is what will keep equipment running better, for longer, and with fewer maintenance updates.
Types of Hydraulic Filters and Systems
There are several types of hydraulic filters based on their position within the system. The filter housings, which are engineered for a variety of pressure ratings, contain a filter element which absorbs contaminates and is switched out when full. Multiple types of filter may be used depending on factors like component sensitivity or great amounts of ambient contamination.
In-Line Filtration
An in-line filter is a filter unit which is plumbed directly into the hydraulic system. These filters operate when the hydraulic machine is active, filtering the hydraulic fluid as the system is in operation and protecting the hydraulic pump and other vital components from contaminate wear.
There are a variety of in-line filters designed to function at various points in a system, such as the hydraulic fluid reservoir and return lines. They come in two basic forms: spin on filters and cartridge filters.
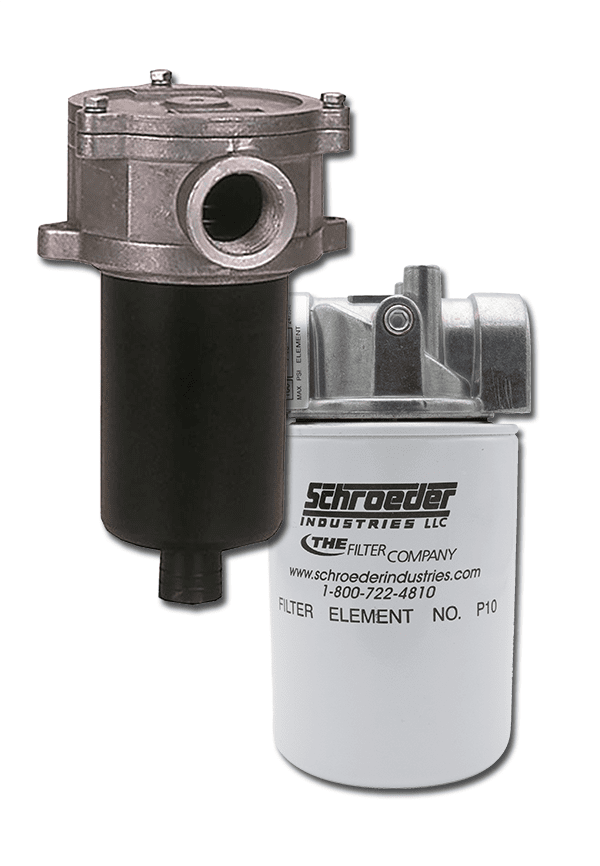
- Cartridge Filters include three separate components: the head (which attaches directly to the system), the filter element (which traps contaminates and filters the fluid), and the cartridge bowl (which threads onto the head and contains the filter element). When the filter is full, only the filter element is discarded and replaced. Cartridge filters can be more challenging to change, and are subject to possible damage and wear in the process, but are overall more cost efficient and less wasteful than spin on filters.
- Spin On Filters combine the cartridge bowl and filter element into a single unit. This unit is screwed onto the hydraulic system, and when full, the entire unit is removed, disposed of, and replaced. While spin on filters are very easy and convenient to switch out compared to cartridge filters, they result in much more more waste when thrown away.
Offline Filtration
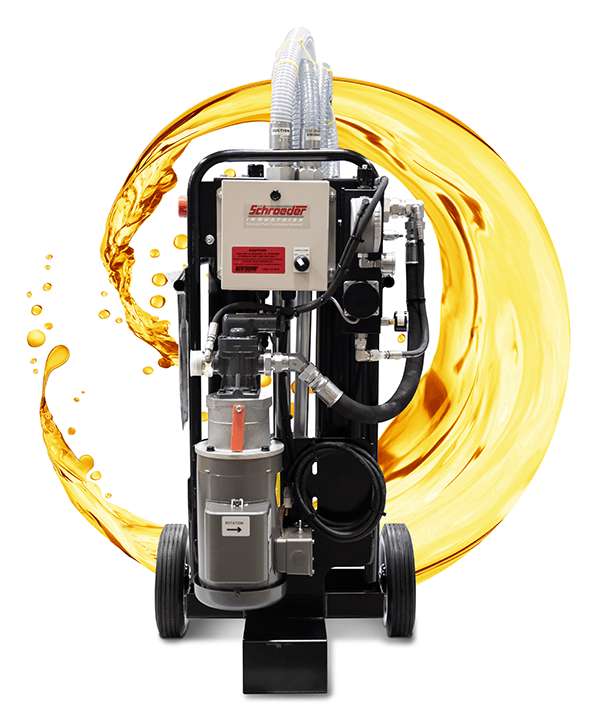
While in-line filters are more typical, stand-alone units that operate offline and away from the hydraulic application are also effective in contamination control. Offline filter systems, such as hydraulic filter carts, are commonly used to enhance the in-line filtration and are not meant as replacements.
Their main advantage over an in-line filtration system is that they can be used even when the hydraulic equipment is not active. Equipped with a pump-motor group of their own, offline oil conditioning units do not require the power of a hydraulic machine. They are their own independent system.
Oil conditioning units are typically used for the conditioning of stored fluid, fluid dispensing applications and transferring processes. It is basically summed up that everywhere the fluid is not flowing through a system, it should be accompanied by a hydraulic filter cart.
Filter Elements
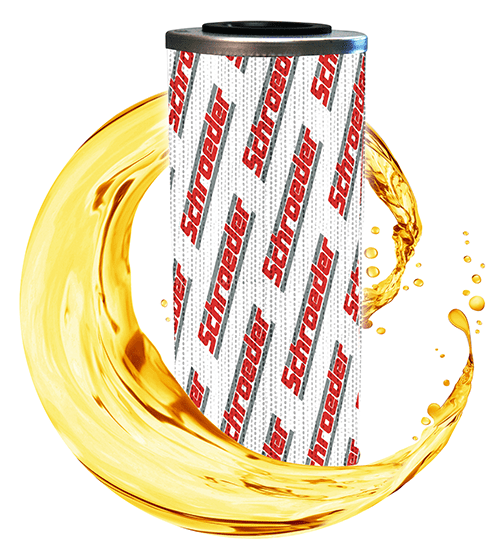
Filter elements are the heart and soul of every hydraulic fluid filtration system. Depending on the type of contamination affecting a system, there is a wide variety of filter elements engineered for various filtration challenges.
Elements can be manufactured to filter various particulate sizes, capture water, and even reduce static charges that can build up in the hydraulic fluid. For clean fluid, choosing a high quality filter element is one of the most important considerations.
Hydraulic Filtration Solutions from Schroeder Industries
Want to protect your valuable hydraulic equipment? Schroeder Industries offers a full range of filtration solutions, backed by decades of proven quality and innovation in the field of fluid filtration. Contact us for more information on how our hydraulic filtration products can enhance your equipment.
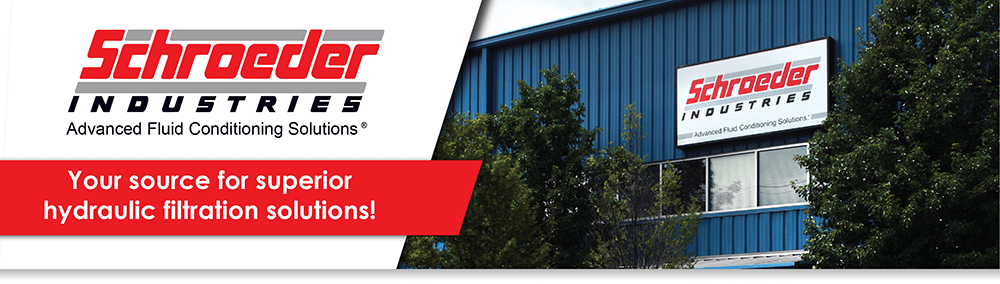